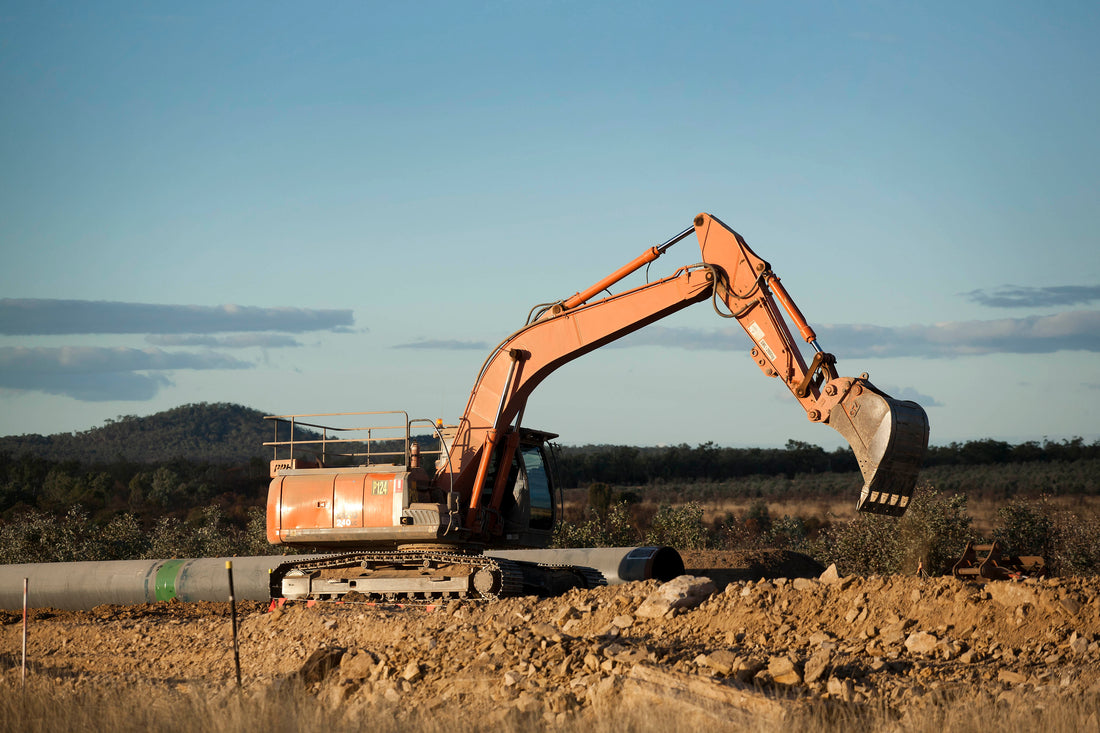
< BACK TO News
Six items to check when selecting a sieve bucket for a backhoe or excavator
When you’re screening, sieving and sorting materials (such as sand, slag, bricks and rubble) you need a screening or sieve bucket that’s going to go the distance. Here is a quick 6-item checklist you can use to ensure you get the best possible sorting bucket for your application.
- Bottom-end strength The sieve bucket should be built so that the baseplate and curved backplate form a rigid composite beam that provides sufficient bottom end strength to support or carry the load across the entire width of the bucket and give years of trouble free operation.
- Bucket shape The sorting bucket shape should promote efficient loading of material. Look for screening buckets with the right width / capacity combination to suit the material density, truck or bin capacity and digging conditions of your application.
- Bucket designDepending on the material you need to move (rock, coal, gravel, sand or even hot materials such as steel slag, a sieve bucket that is designed to suit your particular purpose and built from robust materials will ensure increased capacity, reliability and durability.
- Ribs and apertures Interlocking ribs allow finer material to fall through the sorting bucket while bigger materials (such as bricks and rubble) are retained. It is therefore important to select an aperture size that suits the materials you intend to sort.
- Short pin-to-point A short pin-to-point ensures better digging (bucket breakout force).
- Cutting edge and side cutting edges Effective digging requires good penetration of the bucket into the material it is handling. This is determined largely by the shape of the cutting edge and the side cutting edges.The cutting edge on sieve buckets for excavators can be fitted with either teeth and adaptors or bolt-on-edge.Depending on your application, screening buckets can be fitted with side wear patches and corner-wear strips to reduce wear and tear on the sorting bucket.